Proceso de fabricación de TEMO :
Inyección de plástico
TEMO es una nueva solución de propulsión eléctrica para barcos que se inspira en la movilidad urbana y la electroportabilidad.
Diseñado en 2019, desarrollado en colaboración con la oficina de diseño CIMTECH en Rennes y luego industrializado por el acelerador Axandus en Carquefou en Loire-Atlantique, TEMO encontró rápidamente su mercado y se prepara para entregar nada menos que 500 unidades en este primer año de lanzamiento.
Entre los atractivos argumentos de este nuevo motor, contamos su ligereza, su diseño único y también su fabricación made in France, con el 70 % de los componentes provenientes de los mejores expertos en un radio de 100 km de Nantes y con un claro enfoque en la calidad. TEMO ha optado por soluciones de fabricación local, con un coste de producción de +15 % frente a las soluciones asiáticas. Una elección asumida por la startup y que parece agradar a navegantes y pescadores, muchos de los cuales reservaron su TEMO incluso antes de las primeras entregas.
“Obtener las piezas terminadas en una sola operación”
Denis Luneau - Director
Entre los expertos que acompañaron la fabricación del propulsor se encuentra la vandeana ASM protoplast.
Responsable de la fabricación de todas las piezas de plástico que componen TEMO, fue elegida por la calidad del diálogo, la seriedad de los equipos, la cercanía del taller, su especialización en inyección y su experiencia de trabajo con startups innovadoras.
Denis Luneau, el director de la empresa, nos habla de este proyecto llevado a cabo en un tiempo récord.
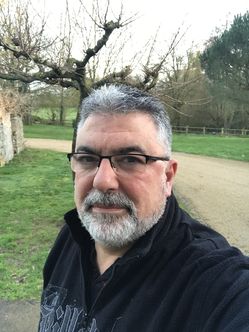
Hola Denis, ¿qué es exactamente ASM?
ASM es un pequeño grupo de 3 entidades creado en 2007 y compuesto hoy por 48 empleados :
- ASM Concept es una oficina de diseño
- ASM France es un taller técnico de fabricación de moldes dedicado a las grandes series.
- ASM Protoplast es un taller de inyección y prototipado
Nosotros efectuamos la parte de « moleado » integrado en inyección de plástico para poder producir y calificar todas las herramientas, procesos y productos que se nos encomiendan.
Una vez producido el instrumental y tras haber validado las muestras iniciales, estamos en condiciones de gestionar la producción en su fase de arranque o producción en serie si corresponde en volúmenes de 100 a 30.000 productos al año.
A partir de estos volúmenes, es otra organización, “la de los fabricantes de inyectoras o equipos”, que también puede ser cliente de ASM France para la producción de moldes en serie.
¿Cuál era su misión para TEMO?
Teníamos una relación a través de la empresa AXANDUS. TEMO buscaba una empresa local capaz de realizar la fabricación de las herramientas como la producción de piezas de plástico.
Integramos este proyecto en la fase final de diseño del producto, cuando la oficina de diseño CIMTECH pudo integrar nuestras limitaciones de producción sin tener que rehacer sus conceptos y validamos con TEMO y AXANDUS los ajustes necesarios para reducir el coste de las herramientas sin degradar la calidad de las funciones del producto.
El hecho de integrar la fase de diseño de producto nos permitió iniciar el diseño de los moldes en tiempo enmascarado (durante la producción y validación de los prototipos producidos en impresión 3D por TEMO). Esto nos permitió comenzar a mecanizar el día después de la consecución de las herramientas.
Se necesitaron 5 moldes para producir 7 productos, incluida la boquilla, que es quizás la parte más compleja de crear. Esta pieza se inyecta en 2 fases y con 2 materiales. En un primer molde, inyectamos el inserto, que se coloca en un segundo molde donde se sobremoldeará con un segundo material. Esta última operación finalizará la ergonomía del producto, garantizará la flexibilidad y la resistencia a los golpes para garantizar la función principal de proteger la hélice.
Estos moldes se fabricaron en un plazo de 6 a 8 semanas, durante el período de vacaciones. Finalmente, después de las primeras partes llamadas, “JOD”, necesitábamos de 4 a 6 semanas de desarrollo de productos y procesos para validar las muestras iniciales “MI”.
¿En qué consiste la inyección de plástico?
La inyección de termoplásticos permite obtener piezas acabadas de formas complejas en una sola operación, con una elección de acabados muy amplia. El 85 % de los materiales inyectados se pueden volver a moler, refundir y reinyectar. Por tanto, esta técnica satisface todos los principios de la economía circular. Los materiales elegidos en el proyecto TEMO han sido validados con este requisito.
El proceso utiliza varios medios de producción: necesitamos el material correcto, la prensa correcta, el molde correcto y los medios periféricos correctos (calentador, robot, hornos...). Todos estos medios deben configurarse de forma adecuada, porque tiene un impacto directo en la calidad del producto. Una vez que este proceso ha sido validado y estable, se deben registrar todos los parámetros para poder reproducirlos y producir las siguientes piezas idénticas.
¿Cuán complejo es un proyecto como este?
Antes de nada, lo más importante es comprender completamente las necesidades y validar las funciones de restricción vinculadas a los usos y al medio ambiente. Tras esta parte, tenemos que analizar los riesgos y proponer al grupo las distintas soluciones técnicas y económicas con sus ventajas e inconvenientes.
Este trabajo previo y colaborativo es fundamental, siendo los líderes del proyecto quienes generalmente asumen la responsabilidad del diseño general frente a los usuarios, por lo que también debemos escuchar al resto de socios, quienes, por su parte, también tienen sus propias limitaciones y funciones que garantizar. Como no tenemos que conocer necesariamente todos los detalles de cada responsabilidad, la relación de confianza es fundamental y debe ejercerse en todos los sentidos. Es ahí donde la proximidad cobra todo su sentido, en mi opinión.
Plazos cortos, presupuestos ajustados, piezas técnicamente difíciles de inyectar o sobremoldear, la integración de imanes dentro de los productos, la resistencia requerida de la boquilla sin poder cambiar el diseño ergonómico... todos ellos eran unos desafíos que nos atraían.
ASM quiere ser moderno y ágil. La innovación siempre ha estado en el corazón de nuestras soluciones. Creo que esto nos permite aprender, adaptarnos y mantenernos motivados para hacer nuestro trabajo de una forma natural. La experiencia de Ronan, Stéphane y Jean-Michel, el trabajo de Marie y la visión compartida de Anne Sophie con todo el equipo de ASM PROTOPLAST ha hecho posible colaborar en el éxito de su proyecto y nos enorgullecemos de ello.
A menudo trabajan con startups. ¿A qué se debe?
La colaboración con startups suele consumir mucha energía y, a veces, un relativo riesgo financiero, pero en contacto con ellas aprendemos mucho sobre estrategia empresarial, la importancia de la comunicación, el marketing, poner la experiencia en primer plano... nos ayuda a adaptarnos y a cambiar nuestra visión de nuestro propio ecosistema.
El producto TEMO nos interesó porque es técnico, estético, innovador y está dirigido por Alexandre y su equipo, con quienes compartimos los mismos valores y, en particular, el de haber entendido el interés de producir localmente.
Denis, el plástico no es muy ecológico. ¿Qué opinas al respecto?
No estoy seguro de que el problema sea el plástico. El problema son los materiales de un sólo uso y el consumo excesivo de los mismos, ya sea madera, cartón, plástico o cualquier otro.
Todos los materiales que se han utilizado en el producto TEMO se pueden volver a moler y reinyectar para fabricar otros productos. Por otro lado, a pesar del exigente entorno que supone el medio marino, tienen una vida útil de más de 10 años. Esto no tiene nada que ver con los plásticos de embalaje de tipo “PET” que, de hecho, son difíciles de reciclar y se producen en volúmenes demasiado grandes.
Y aquí es donde cobra importancia el ecodiseño que se hizo con CIMTECV para que el producto fuera desmontable, reparable y reciclable. Seguimos trabajando con TEMO: actualmente estamos haciendo pruebas de materiales para desarrollar ciertas piezas inyectadas con plástico reciclado. Por otro lado, es necesario que el sector siga progresando y se organice. Existe una fuerte demanda y los precios de los materiales reciclados son a veces más caros que el material básico y para funciones técnicas inferiores...
¡Gracias, Dennis!
Denis Luneau, director de ASM protoplast
Artículos relacionados :
De la idea al producto - #1: El diseño