Processus de fabrication TEMO :
L'injection plastique
Inspiré par la mobilité urbaine et l'électro-portabilité, TEMO est une nouvelle solution de propulsion électrique pour bateau.
Conçu en 2019, développé ensuite en partenariat avec le bureau d’étude CIMTECH à Rennes puis industrialisé par l’accélérateur Axandus à Carquefou en Loire-Atlantique, TEMO a très vite trouvé son marché et s’apprête à livrer pas moins de 500 unités dans cette première année de lancement.
Parmi les arguments séduisants de ce nouveau moteur, on compte sa légèreté, son design unique et également sa fabrication made in France avec 70% des composants sourcés chez les meilleurs experts dans un rayon de 100KM autour de Nantes, et dans une démarche de qualité. TEMO a choisi des solutions de fabrication locales, moyennant un coût de production de +15% versus des solutions asiatiques. Un choix assumé par la startup et qui semble trouver écho chez les plaisanciers et pêcheurs, nombreux à avoir commandé TEMO avant même les premières livraisons.
“Obtenir en une seule opération des pièces finies”
Denis Luneau - Directeur
Parmi les experts qui ont accompagné la fabrication du propulseur se trouve le vendéen ASM protoplast.
Responsable de la fabrication de toutes les pièces en plastique qui composent TEMO, il a été choisi pour la qualité du dialogue, le sérieux des équipes, la proximité de l’atelier, son savoir-faire en injection ainsi que son expérience de travail avec des startups innovantes.
Denis Luneau, le directeur de l’entreprise nous parle de de ce projet réalisé dans des délais record.
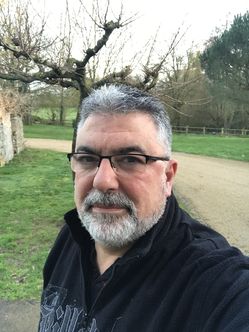
Bonjour Denis, ASM c’est quoi au juste ?
ASM est un petit groupe de 3 entités, créé en 2007 et composé aujourd’hui de 48 salariés :
- ASM Concept est un bureau d’étude
- ASM France est un atelier de fabrication de moule technique dédié plutôt à la grande série
- ASM Protoplast est un atelier d’injection et de prototypage.
Nous sommes « mouliste » intégré en injection plastique afin de pouvoir réaliser et qualifier tous les outillages, les process et les produits qui nous sont confiés.
Une fois les outillages réalisés et après avoir validé les échantillons initiaux, nous sommes en mesure de gérer la production dans sa phase d’amorçage ou de vie série si celle-ci correspond à des volumes de 100 à 30 000 produits par an.
Au-delà de ces volumes, c’est une autre organisation, « celle des injecteurs ou équipementiers » qui peuvent être en outre les clients d’ASM France pour la réalisation des moules grande série.
Quelle a été votre mission pour TEMO ?
Nous avons été mis en relation via la société AXANDUS. TEMO recherchait une société locale capable de réaliser à la fois les outillages et la production des pièces plastiques.
Nous avons intégré ce projet dans la phase finale de conception produit, le bureau d’étude CIMTECH a pu intégrer nos contraintes de réalisation sans avoir à refaire ses concepts et nous avons validé avec TEMO et AXANDUS, les aménagements nécessaires pour réduire le coût des outillages sans dégrader la qualité des fonctions produit.
Le fait d’intégrer la phase de conception produit nous a permis de démarrer la conception des moules en temps masqué (pendant la réalisation et la validation des prototypes réalisés en impression 3D par TEMO). Ce qui nous a permis ensuite de démarrer les usinages dès le lendemain du « top Réalisation Outillage ».
5 moules ont été nécessaires pour réaliser 7 produits, dont la tuyère qui est peut-être la pièce la plus complexe à réaliser. Cette pièce est injectée en 2 phases et avec 2 matières, nous injectons l’insert dans un 1er moule puis cet insert est ensuite placé dans un 2ème moule ou il va être surmoulé d’une 2ème matière. Cette dernière opération va finaliser l’ergonomie du produit, garantir la flexibilité et la tenue aux chocs afin de garantir la fonction principale de protéger l’hélice.
Ces moules ont été réalisés dans un délai de 6 à 8 semaines, pendant la période de congé. Enfin, après les toutes premières pièces appelées « IOD » nous avons eu besoin de 4 à 6 semaines de mise au point produit et process pour valider les échantillons initiaux « EI ».
Ça fonctionne comment l’injection plastique ?
L'injection thermoplastique permet d'obtenir en une seule opération des pièces finies, de formes complexes, avec un choix de finition très large. 85% des matières injectées peuvent être rebroyées, refondues et réinjectées. Cette techno rentre donc complètement dans les principes d’économie circulaire. Les matières choisies dans le projet TEMO ont été validées avec cette exigence.
Le procédé fait appel à plusieurs moyens de production : il nous faut la bonne matière, la bonne presse, le bon moule, et les bons moyens périphériques (réchauffeur, robot, étuves). Tous ces moyens doivent être réglés et ses réglages ont un impact direct sur la qualité du produit. Une fois ce processus validé et stable, il faut enregistrer tous les paramètres afin de pouvoir les reproduire et réaliser les prochaines pièces à l’identique.
Quelle est la complexité d’un projet comme celui-ci ?
Le plus important est d’abord de comprendre parfaitement les besoins et de valider les fonctions de contrainte liée aux usages, à l’environnement. Suite à cette écoute, il nous faut analyser les risques et proposer au groupe les différentes solutions technico-économiques avec leurs avantages et leurs inconvénients.
Ce travail préalable et collaboratif est indispensable, avec les porteurs de projet qui soutiennent généralement la responsabilité de la conception globale vis-à-vis des utilisateurs, nous devons donc aussi écouter les autres partenaires qui ont aussi leurs propres contraintes et fonctions à garantir. Sans forcément connaître tous les détails de chaque métier, la relation de confiance est donc primordiale, elle doit s’exercer dans tous les sens et c’est pourquoi, à mon avis, la proximité prend tout son sens…
Les délais courts, les budgets serrés, les pièces techniques difficiles à injecter, à surmouler, l’intégration d’aimant à l’intérieur des produits, la résistance demandée de la tuyère sans pouvoir changer le design ergonomique sont des challenges qui nous ont intéressé.
ASM se veut moderne et agile. L’innovation a toujours été au cœur de nos solutions, je pense que cela nous permet d’apprendre, de nous adapter, et de rester tout simplement motivé à exercer notre métier. L’expertise de Ronan, de Stéphane et de Jean-Michel, le travail de Marie et le regard croisé d’Anne Sophie avec toute l’équipe ASM PROTOPLAST a permis de collaborer au succès de votre projet et nous en sommes très fiers !!!
Vous travaillez souvent avec les start-up, pourquoi ?
La collaboration avec les start-ups est souvent énergivore et parfois un peu risquée financièrement, mais à leur contact nous apprenons beaucoup, sur la stratégie commerciale, l’importance de la communication, le marketing, la mise en évidence des savoir-faire … Cela nous aide à nous adapter, à changer notre regard sur notre propre écosystème.
Le produit TEMO nous a intéressé, car il est technique, esthétique, innovant et porté par Alexandre et son équipe avec qui nous partageons les mêmes valeurs notamment celle d’avoir compris l’intérêt de produire localement.
Le plastique n’est pas très eco friendly Denis, vous en pensez quoi ?
Je ne suis pas sûr que la problématique soit le plastique, le problème : c’est l’usage unique et la surconsommation des matériaux que ce soit du bois, du carton, du plastique ou tout autres matériaux.
Toutes les matières qui ont été utilisées dans le produit TEMO peuvent être rebroyées et être réinjectées pour réaliser d'autres produits. D’autre part et ce malgré le milieu sévère qu’est le milieu marin ils ont une durée de vie de plus de 10 ans. Cela n’a rien à voir avec les plastiques d’emballage type « PET » qui sont en effet difficilement recyclables et produit en volume beaucoup trop important.
L'Éco-conception qui a été faite avec CIMTECH pour rendre le produit démontable, réparable, recyclable a du sens. Et nous continuons à travailler avec TEMO, nous réalisons actuellement des tests de matériaux afin de faire évoluer certaines pièces injectées en plastique recyclé. Par contre, il faut ensuite que la filière suive et s’organise. La demande est forte et les prix des matières recyclées sont parfois plus chères que la matière de base et pour des fonctions techniques inférieures…
Merci Denis !
Denis Luneau, directeur d'ASM protoplast
Articles liés :
De l'idée au Produit - #1 : Le Design